CLIENT BACKGROUND
A multinational manufacturer of specialised polymer systems sought enhanced machine safety.
Our customer manufactures industrial motion components, high-tech coated fabrics, and air and fluid handling systems based on based on reinforced polymer technology. Their customer base spans the aerospace, automotive, food processing and general industrial, logistics, materials processing sectors. They are part of a larger multinational group.
THE CHALLENGE
Ageing systems and imported US machinery required reengineering to meet modern British safety standards.
An internal audit had revealed to our customer that some of their older systems, whilst still functional and productive, no longer met modern safety standards. Additionally several new machines sourced from the US parent company were due for installation.
The UK based facilities are required to conform to global group operational practices and so for some processes use US-manufactured machinery. While this directive ensures consistency across the group’s global sites, the installation and operation of these systems however presents significant challenges in technical integration and regulatory compliance.
The challenges of installing our customer’s US-made machines into their British factory were twofold. Firstly, the equipment, designed for American electrical systems and safety protocols, needed to be re-engineered to comply with British standards. Secondly, the machinery did not initially meet UK regulations – lacking features such as compliant emergency stops and guarding.
In addition to the challenges of integrating systems from outside the UK and Europe, many of the existing assets in the company’s UK facilities are ageing machines that were designed before modern safety standards were introduced and were no longer compliant with PUWER regulations or current machinery safety standards.
OBJECTIVES
Ensure all machinery is effectively safeguarded and compliant with UK legislation whilst providing an overall safe and effective manufacturing facility.
The project aimed to install effective safeguarding on both legacy and imported machinery, ensuring full compliance with UK safety legislation. In addition to individual machines, the customer required that the manufacturing site as a whole was made as safe and operationally effective as possible.
THE SOLUTION
Both legacy and US equipment were reengineered on-site and off-site to minimise the disruption to manufacturing whilst maximising operating safety.
We reengineered both the new US equipment and the legacy machinery for integration into the customer’s factory. To minimise production disruption, some work was carried out onsite, while other systems were moved to our workshop in Elland, West Yorks for the required modifications to be completed.
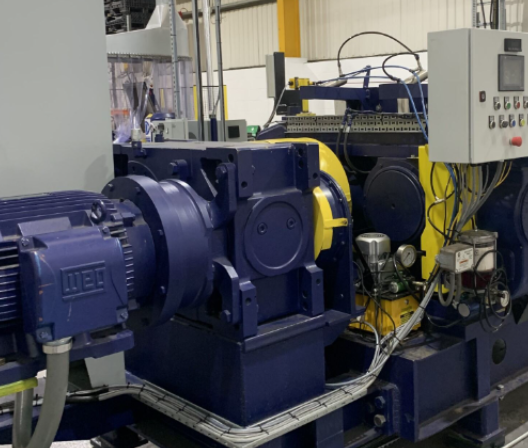
The US machines, originally designed for an American electricity supply, were modified to comply with EN60204-1 Safety of machinery – Electrical equipment of machines. Components were upgraded to accept a 230V/50Hz power supply rather than the original US supply.
Updating older equipment necessitated the sourcing or fabricating of obsolete parts and redeveloping control systems to meet current standards such as EN13849-1 Safety of machinery – Safety related parts of control systems; Part 1: General principles for design.
Upgraded interlocking functions, emergency stop devices and enhanced guarding were fitted to both older and imported equipment to improve safety and comply with applicable standards All modifications were executed in close consultation with our customer to align with production schedules, sometimes requiring work outside standard hours.
RESULTS AND BENEFITS
Full compliance and enhanced operational safety achieved for all machinery and the factory as a whole.
Safety Systems Technology issued declarations of conformity to indicate compliance of the upgraded machinery in accordance with the relevant standards as required by the Machinery Directive 2006/42/EC and so were able to assure regulatory compliance for the machinery modified and updated.
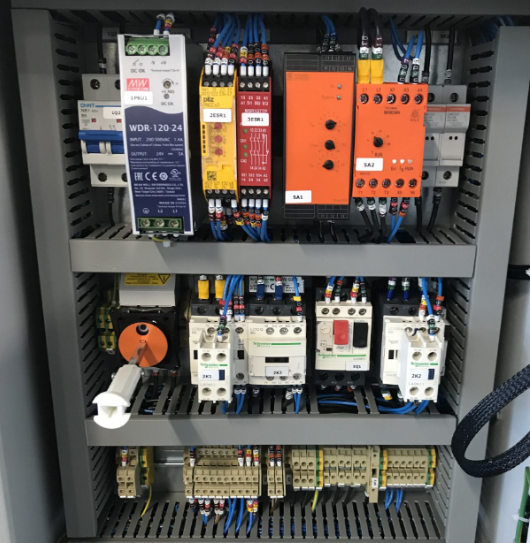
The implementation of electrical and mechanical guarding provided an optimal level of industrial safety with specific compliance to EN60204-1 for overall electrical safety and EN ISO13849-1 for safety related control functions.
This project ensured that all the equipment used in the manufacturing operation in our customer’s UK facilities was safe, operationally efficient, reengineered to the highest of standards ensuring PUWER compliance and configured to allow optimal manufacturing efficiency. In addition, we were able to take a holistic view and improve the efficiency and safety of the facility as whole, not solely that of individual machines.
CONCLUSION
Flexible execution delivered a compliant and efficient manufacturing facility on schedule and within budget.
Our customer was delighted to have all manufacturing equipment and the overall environment brought up to a consistent level of compliance, operational efficiency and operating safety. Working flexibly, sometimes out of hours, and updating some equipment in our own workshops meant we were able to deliver this project to schedule and to budget.