Guarding design is a key factor in machinery safety compliance, hence getting it right first time is of paramount importance. In this research article, we will explore why thoughtful guarding design matters for machinery safety compliance.
Read more: Why Thoughtful Guarding Design Matters for Machine Safety Compliance
Picture this, a scenario that occurs every day across manufacturing floors in the UK: an operator reaches to clear a blockage, temporarily removing a guard to access the machinery. A simple move, but one which has implications for both safety and productivity. Machine guarding isn’t just about compliance; it’s about protecting lives while maintaining operational efficiency.
PUWER regulations and the range of BS/EN and ISO machinery safety standards provide essential frameworks to ensure machinery is safe and compliant but effective machine guarding goes beyond meeting the essential requirements of the standards alone. It represents an investment in terms of making commitments to employee welfare, improving operating efficiency and being proactive about safety. This is why thoughtful guarding design matters for machine safety compliance, because thoughtful guarding design is critical to increasing output without compromising safety.
The Real Cost of Poor Guarding
The conversation around machine guarding often focuses solely on regulatory compliance. The true cost of inadequate guarding however, extends far beyond potential HSE penalties. We worked with a mid-sized manufacturing operation that had experienced a serious injury when an operator bypassed a poorly designed guard to clear material as in the scenario above. In this example, the immediate costs included production shutdown to allow for investigation, equipment repair, and employing temporary cover staff totalling approximately £30,000 in direct expenses.
The longer-term costs however, proved even greater: insurance premiums increased, retrofitting redesigned guards across similar equipment required investment which hadn’t been budgeted for. In addition the company faced heightened HSE scrutiny for many months afterward.
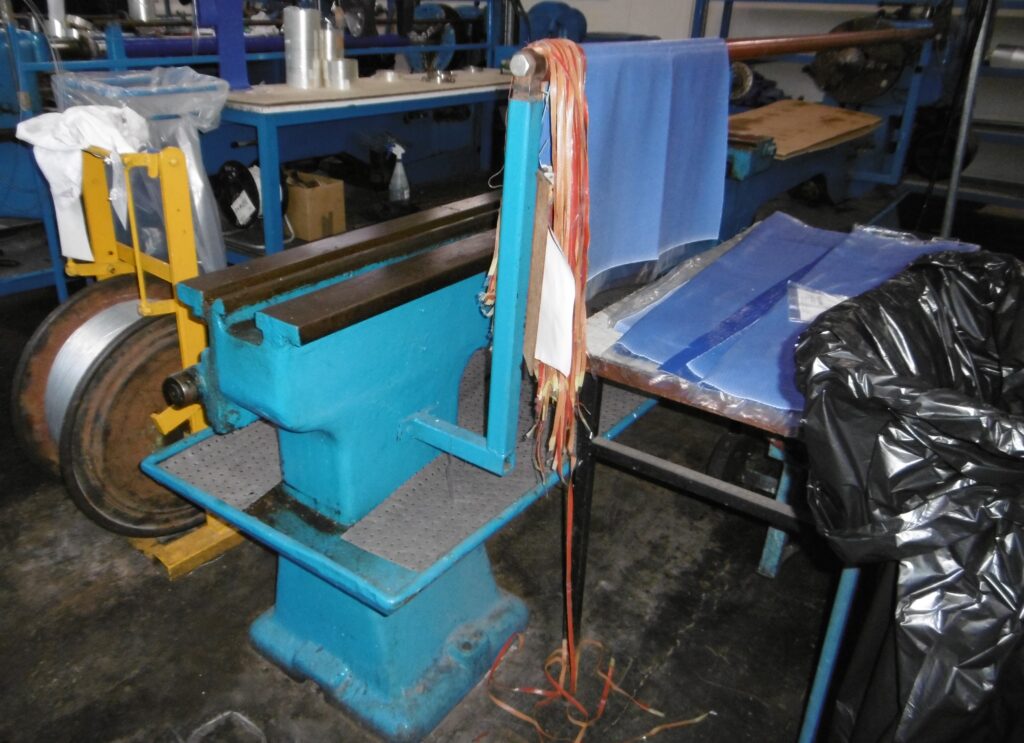
Most concerning was the cost to workforce morale, with a number of skilled operators seeking employment elsewhere due to safety concerns.
These costs were easy to measure. The hidden cost of reputational damage that affected customer relationships and recruitment has been harder to gauge. When procurement managers evaluate suppliers, safety incidents raise red flags about operational stability and reliability. The clear reality is that inadequate guarding doesn’t just risk non-compliance, it threatens business sustainability.
Proactive vs. Reactive Approaches To Machine Guarding Design
The attitude an organisation takes toward machine guarding significantly impacts both safety outcomes and operational efficiency. Consider these two contrasting approaches:
Manufacturer A addresses guarding only after incidents or regulatory inspections. Their guards are theoretically compliant but create workflow obstacles, leading operators to develop workarounds. With machinery modified in this way, guards aren’t then updated until the next scheduled inspection. This approach results in a patchwork of solutions, periods of non-compliance and a workforce suspicious of machine guarding, seeing it as an impediment to productivity.
Manufacturer B however, has integrated guarding considerations into equipment procurement and modification planning. They regularly review guarding effectiveness against both current standards and emerging risks. Most importantly, they involve operators in maintaining and developing safety systems. Staff are directly involved in reviewing set-ups and testing new guards before wider implementation. As a result, the company experiences lower accident rates, minimal production disruptions for safety modifications and a workforce that actively participates in safety improvements rather than trying to circumvent them.
Companies using machinery which adopt such proactive approaches can reduce overall compliance costs while improving productivity metrics. They are clear that thoughtful guarding design delivers return on investment beyond regulatory compliance.
The Human Element in Machine Guarding Design
As we’ve said, guarding is about much more than just compliance. The ergonomics of how a machine is used and how it fits into the operation in a given facility must be accounted for. We came across a case at a precision engineering facility in the Midlands, where a newly installed machine had been supplied with fixed guards that met all relevant standards. Just weeks after installation and commissioning however, operators had developed unofficial modifications to improve visibility and reduce the time needed for routine adjustments. This case highlights a crucial truth: guards designed without the operator or maintenance engineers in mind often become obstacles to efficient work and drive misuse which is actually foreseeable.
Thoughtful guarding design recognises that protection systems must work with human behaviour, not against it. This means considering
- Visibility requirements for monitoring processes without removing guards.
- Access frequency for maintenance and adjustments. Physical effort required to use guards properly.
- How many steps are necessary to follow safety procedures.
We helped one customer address these factors by replacing fixed panels with interlocked guards on frequently accessed areas. This simple change reduced maintenance time by 30% while eliminating the temptation to bypass safety systems. Acceptance of this solution was made easier and longer lasting by involving operators in design modifications from the outset rather than simply imposing it without consultation.
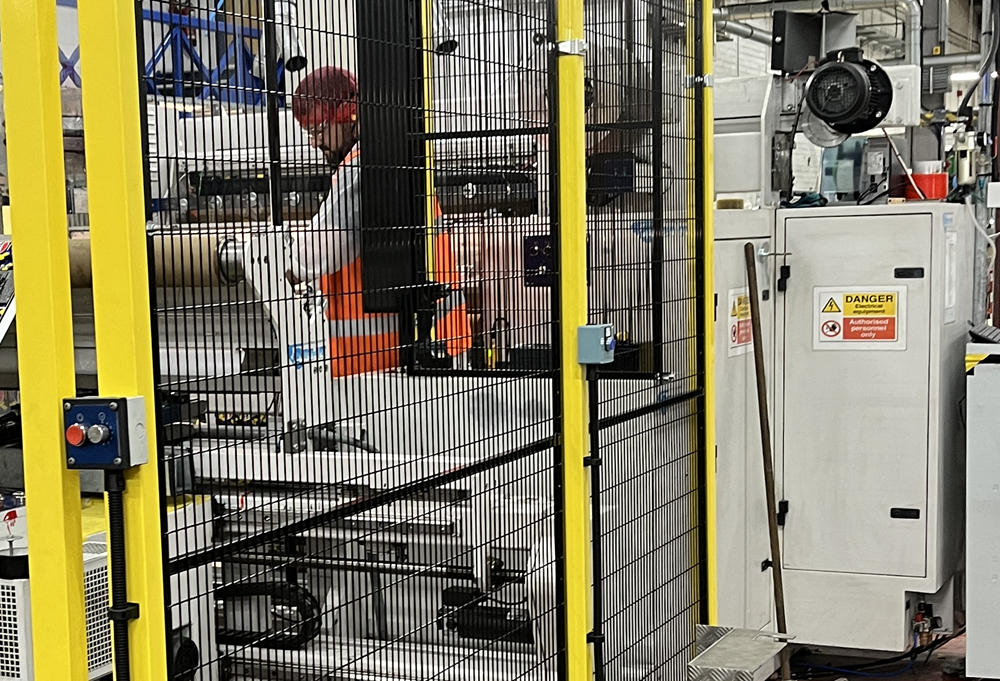
The lesson is clear, guards designed with human factors in mind protect more effectively because they’re more consistently used. Machine safety and engineering teams that collaborate with shop floor employees develop solutions that balance safety with practicality, creating sustainable compliance. This is true in a variety of settings and wherever machinery is used, across a wide range of manufacturing, engineering and heavy industry plants through to warehousing and fulfilment facilities.
Comprehensive Machine Guarding Solutions Under PUWER
PUWER (Provision and Use of Work Equipment Regulations) clearly mandates that machinery must be safe for use, maintained in a safe condition and used only by people who have received adequate training. These regulations have evolved since their introduction in 1998, with amendments and updated guidance reflecting advances in machine technology and capabilities and consequentially emerging workplace risks.
For effective compliance with PUWER Regulation 11, organisations must implement safeguarding solutions from a comprehensive range of options according to the hazards associated with a given machine and its operation. Guarding needs to be appropriate to the risk but also practical.
Physical Guards
- Fixed guards: Permanently attached barriers that require tools for removal are ideal for areas requiring infrequent access. PUWER Regulation 11(2)(a) specifically references these as the first line of protection.
- Interlocked guards are connected to machine control systems to prevent operation when guards are open and are suitable for areas requiring regular access for tool changes or maintenance.
- Manually adaptable adjustable guards to accommodate different workpiece sizes while maintaining protection. Commonly used on machine tools.
- Self-adjusting guards automatically conform to the size and shape of materials being processed, offering continuous protection during a range of operations.
The Relationship Between PUWER and Machinery Safety Standards
When it comes to designing machine guarding it’s important to understand the symbiosis between PUWER Regulations and relevant machinery safety standards. While PUWER establishes the legal requirement for adequate guarding, the comprehensive range of both BS/EN and ISO standards provide detailed technical specifications on how guards should be designed, constructed, and positioned. EN ISO 14120 for example provides general guidance on guarding design and construction considerations such as
- Material selection criteria for various industrial environments
- Ergonomic considerations to prevent operator guard bypass.
- Guard fixing systems and their security requirements.
- Human elements
- Construction aspects
- Testing requirements.
It is important to remember that wherever a specific Type C standard exists for machinery then this standard should take precedence over Type A and B standards.
Used in conjunction with each other, PUWER regulations and relevant standards enable a comprehensive approach that not only ensures legal compliance but also promotes practical, effective safeguarding solutions that both protects workers and also increases productivity.
Building a Future-Proof Guarding Strategy
Developing an approach to guarding that is sustainable and remains effective as your operations evolve requires structured planning.
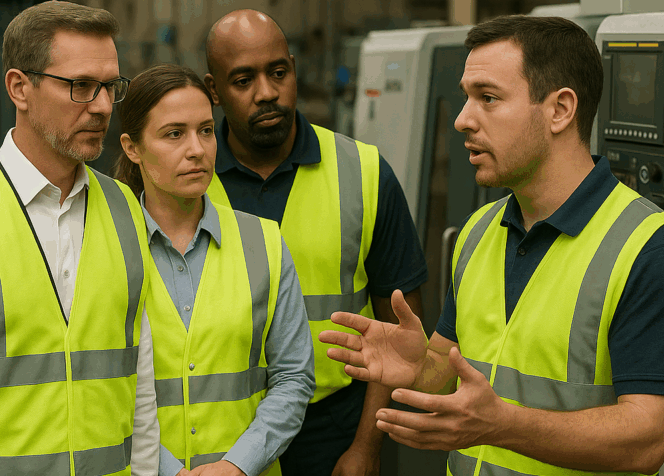
Proactive machine guarding management should be a four step process.
- Risk assessment and gap analysis;
Operation-specific risk assessments rather than generic evaluations should be undertaken for all machinery. This involves observing and understanding actual work practices on equipment during different shifts, with different operators and production scenarios. In this way it’s possible to identify the potential conflict between standard guarding and operational demands. Secondly a thorough and targeted gap analysis against the relevant standards can reveal opportunities for guarding improvements that enhance both safety and efficiency. It is important that all forms of risk assessment are undertaken by competent persons. - Operator input to the guarding design process;
The establishment of a formal process for operator input on guarding designs doesn’t mean compromising safety standards. Rather practical modifications that maintain protection while improving usability are identified. Ideally those responsible for managing health and safety will facilitate the creation of cross-functional teams of shop floor operators, maintenance staff and safety specialists to evaluate new guarding requirements and solutions before full implementation. - Synchronising maintenance and guarding updates;
Aligning guarding updates with planned maintenance schedules minimises disruption to production. Some manufactures and equipment operators create rolling plans for guarding reviews and updates. These plans coordinate with equipment lifecycle management. This approach transforms safety compliance from a reactive expense to a planned investment. - Exploring new innovations;
It’s worth the effort to keep up to date with development in guarding technology. AOPD (active optoelectronic protective device)-based products, programmable safety systems, and augmented reality for training for example, can all complement traditional physical guards to create more comprehensive protection with less impediment to productivity. Evidence has shown that even modest investment in some of these emerging technologies can result in significant improvements in both safety outcomes and operational efficiency.
Contact Safety Systems Technology For Your Machine Guarding Needs
Effective machine guarding of course depends on thoughtful design but also serves to provide more than regulatory compliance. Adopting an inclusive, proactive and holistic approach demonstrates an active commitment to workforce protection and enabling operational excellence. Organisations which see guarding as a strategic investment rather than a regulatory burden consistently outperform their competitors in both safety metrics and productivity.
The ethos of continuous improvement applies just as much as to guarding as it does to operational processes in general. Successful manufacturing, heavy industrial and logistical operations all recognise that effective guarding requires ongoing attention and adaptation. Involving the workforce, planning proactively and adopting innovative solutions to safety compliance changes means that effective guarding morphs from being a cost centre to become a competitive advantage.
Safety Systems Technology partners organisations across a broad range of manufacturing and other industries to design, install and maintain machine and electrical guarding. Our customers rely on our expertise to ensure they stay compliant and employ optimum safety solutions. Get in touch today to discuss your machinery safety requirements.