CLIENT BACKGROUND
A longstanding Northern Ireland factory, now part of a multinational group, required enhanced safety measures for some of its aging equipment.
Our customer has a factory in Northern Ireland producing paper, card and fabric packaging for bulk agricultural goods and animal feeds. The factory has been around for many decades under different ownership. Over time the independent company has become part of a multinational diversified group.
THE CHALLENGE
An audit revealed critical HSE deficiencies and a need for rapid safety updates during a two-week shutdown.
A TÜV SÜD audit commissioned by the European Health and Safety Director exposed multiple machinery safety deficiencies, including older machinery that no longer achieved PUWER requirements or met modern standards. In particular, an 80m animal feed bag manufacturing line, though mechanically sound, had no guarding, compromising worker safety. The necessary updates to this and other machinery had to be completed within a two-week factory shutdown.
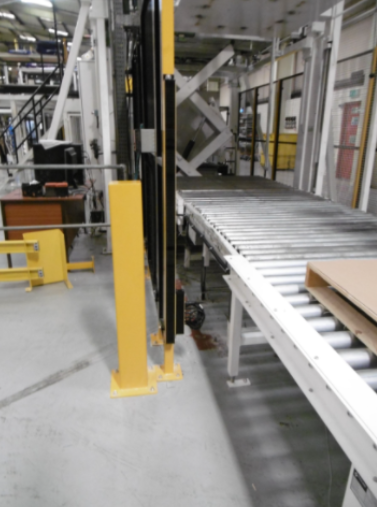
OBJECTIVE
Standardise safety and boost production by exceeding compliance requirements.
The aim was to ensure consistent operating security across the factory and create a safer working environment. Beyond merely ticking regulatory boxes, the customer believed that enhanced safety would also improve production efficiency.
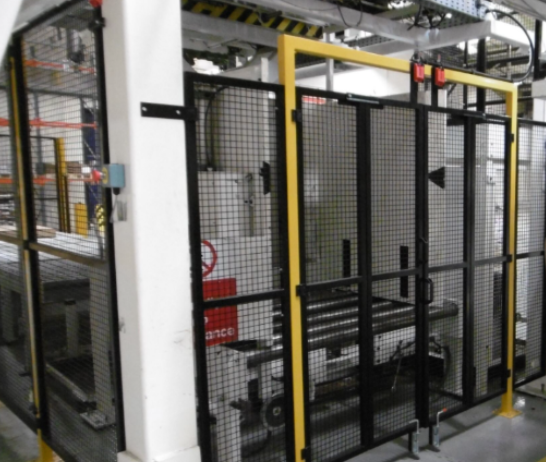
THE SOLUTION
A detailed assessment led to a tailored, on-site solution executed during the shutdown.
Safety Systems conducted a comprehensive site assessment of the working environment and machinery and how it was used by the workforce. Based on this evaluation, we swiftly devised and refined a proposal to update equipment in line with the PUWER Regulations, consulting with the customer at each stage. The work was then executed on-site during the planned two-week shutdown.
RESULTS AND BENEFITS
Accelerated work during a shortened shutdown achieved full regulatory compliance.
When the factory shutdown was reduced to one week due to urgent production needs, we were able to adapt the work schedule and deploy additional resources. Coupled with longer shifts than originally planned, we were able to complete the work in less than half the time originally scheduled.
The result was that all machinery in the plant was compliant with PUWER. Mechanical guards were added where there had been none, a robust interlocking system and upgraded emergency stop controls installed the length of the 80m processing machine and on other machinery in the plant.
CONCLUSION
Agile and flexible resource management delivered safety compliance despite compressed project timeframes.
A flexible allocation of resources combined with a commitment to the needs of the client needs delivered compliant safety solutions despite an unexpected reduction in the time allowed to complete the project.
We were able to react and adjust our resource allocation to meet the customer’s changing needs, delivering compliant safety solutions in less time than originally planned. When the shutdown period was unexpectedly reduced, we deployed additional resources and extended shifts to complete all the required safety upgrades.
The result was that the client achieved full PUWER compliance
across their facility with minimal disruption to their production schedule. This project highlights our commitment to providing effective safety solutions whilst being reactive and responsive to changing operational demands.